Factory Direct Selling UV Coating Plastic Flooring Self Adhesive LVT Flooring Planks
What Is LVT Flooring?
Short for luxury vinyl tile, LVT is designed to replicate hard surface flooring materials such as stone or wood, yet provide many more practical benefits. Available in planks or tiles, LVT uses a realistic photographic print film and a clear vinyl layer that opens up a wide variety of design concepts. Even the most trained of eyes have a hard time distinguishing LVT from the products that it mimics.
To go the extra mile in understanding LVT, let’s take a look at how it’s made. LVT is manufactured through the following five primary processes.
1. Research and Development
From the beginning, research and development teams aim to simulate and evaluate new innovative concepts through trial and error. Large amounts of raw materials are mixed so that the team can study their interactions. The raw materials used in the production of LVT include polyvinyl chloride resins (PVC) and calcium carbonate. Once the team has a satisfactory compound to work with, it is ready to begin the calendering process.
2. Calendering Process
The calendering process uses a series of heated rollers to “roll or squeeze” the compound into a continuous sheet. By manipulating the rolls, the width and thickness of the sheet can be controlled with precise accuracy and consistency. Once the sheet is passed through the heated rolls, it is then sent through a cooling section and sent to lamination.
3. Lamination Process
Through the use of heat and pressure, lamination is a continuous process that bonds one layer to the next until all layers are fully formed. The tiles are constructed of the following four layers:
● Backing layer – Sound absorbing layer with textured grip
● Fill layer – Stability layer for indentation resistance
● Print layer – Certain premium types of LVT come manufactured with realistic, 3D visuals that can be installed to resemble ceramic or stone.
● Wear layer – The wear layer plays a crucial role in the lifespan of your tiles. Clear coatings such as aluminum oxide will keep your flooring from rapidly wearing.
Once the layers are fully formed, the sheet enters into the embossing section.
4.Embossing Process
Here, under heat and pressure, engraved rollers apply the textured design onto the face of the product which can be a light “tick” or a “deep” emboss. Once the texture is applied, the scratch and scuff Top Coat will be applied. The slabs then pass through an annealing oven that uses heated air to raise the temperature of the entire slab to a point that any stress between the layers are relieved. Once cooled back down, this process is added “insurance” to produce a stabilized product that will reduce the opportunity for “doming or cupping” due to stresses between the layers in the finished planks. From there the slabs are pallet and taken to Inspection, the final stop.
5. Inspection Process
During inspection, the slabs are brought into an air controlled room that will maintain the same temperature year round. This is important because it keeps the product in a uniform state during the milling process which helps to ensure consistent milling from one board to the next. Being able to inspect each slab before milling allows technicians to inspect and mark defective areas. The non-defected slabs will then be loaded into the press which offers alternative product sizes and is then sent to milling. Once milled, the product is boxed, wrapped, stacked on a pallet, and ready for shipment.
Product Structure
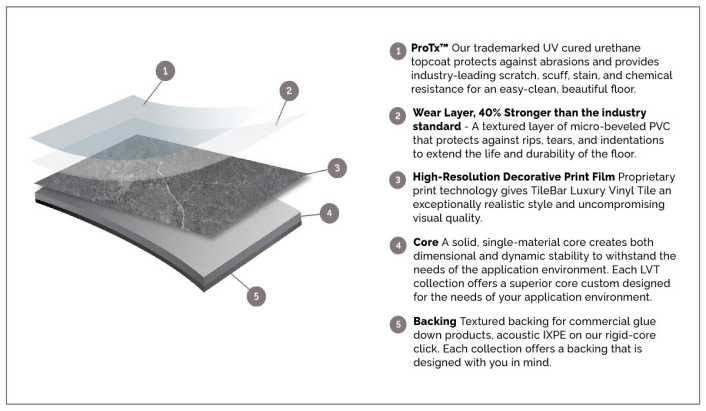

Name | Vinyl flooring (LVT flooring,click LVT flooring) |
Color | Based on 3C lap dip series number or as your samples |
Board Thickness | 2.0mm/2.5mm/3.0mm or customized |
Wearing Layer Thickness | 0.2/0.3/0.5/0.55/0.7 mm or customized |
Surface Texture | Deep Grain,Wood Grain,Marble Grain,Stone,Carpet |
Surface Treatment | UV-Coating |
Installation | Click system,Loose lay,Dray Back/Glue Down |
Delivery Time | 15-25 days |
Size | Inch or MM |
914.4*152.4mm*2.0mm, 36pcs/ctn,120ctns/pallet,10pallets/20GP | |
914.4*152.4mm*2.5mm, 30pcs/ctn,120ctn/pallets,10pallets/20GP | |
914.4*152.4mm*3.0mm, 24pcs/ctn,120ctns/pallets,10pallets/20GP | |
457.2*457.2mm*2.0mm,30pcs/ctn,100ctns/pallet,10pallets/20GP | |
457.2*457.2mm*2.5mm,24pcs/ctn,100ctns/pallet,10pallets/20GP | |
457.2*457.2mm*3.0mm,20pcs/ctn,100ctns/pallet,10pallets/20GP | |
Project Solution Capability: | graphic design, total solution for projects, Cross Categories |
Place of Origin | Shandong China |
Product Type | Vinyl Flooring |
Usages | Indoor |
Features | Waterproof,Wear resistant,Anti-slip,Moisture Proof,Fireproof,durable, anti-scratch, anti-bacterial. |
Market | Export to American,Canadian,European Market,Part Asia,Africa Countries.Australia Market |
Warranty | 10 years for commercial and 25 years for residential |
Material | PVC, Recycle |
Certificate | CE, ASTM, Floor score, Green Guard, GB, ISO9001 |
Supply Ability:10000 Square Meter/Square Meters per Day
Lead time:
Quantity (square meters) | 1 - 1000 | 1001 - 2000 | 2001 - 5000 | > 5000 |
Lead time (days) | 10 | 20 | 30 | To be negotiated |
Packaging & delivery
Packaging Details: Carton+Pallet
Port: Qingdao
Hot Sale Color
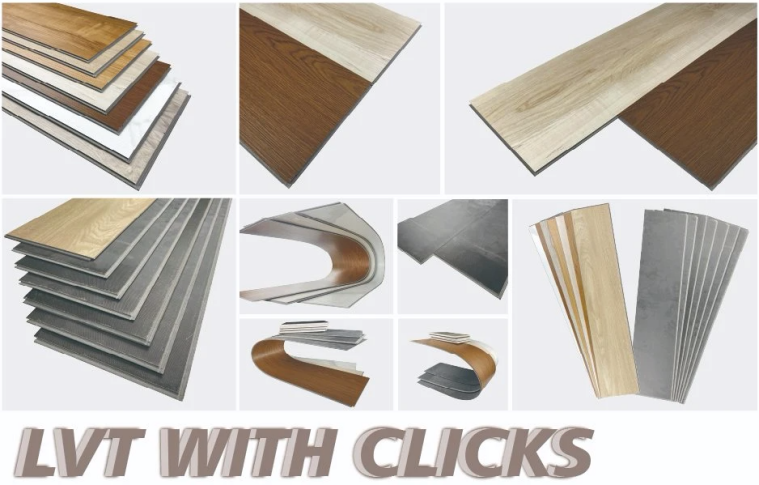
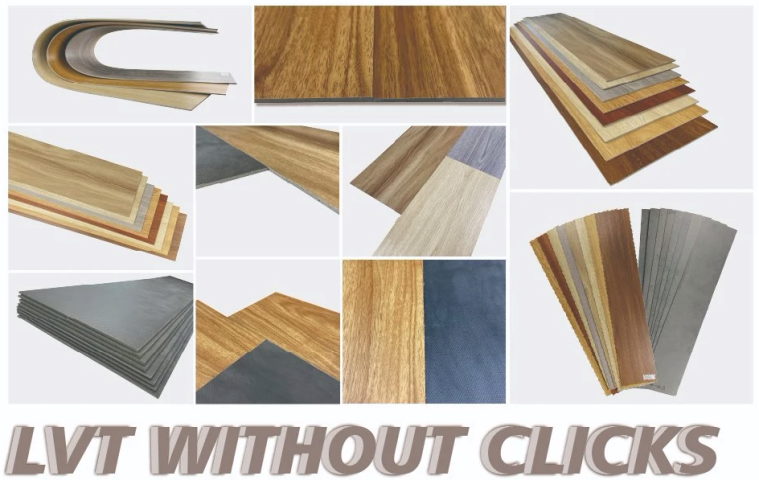
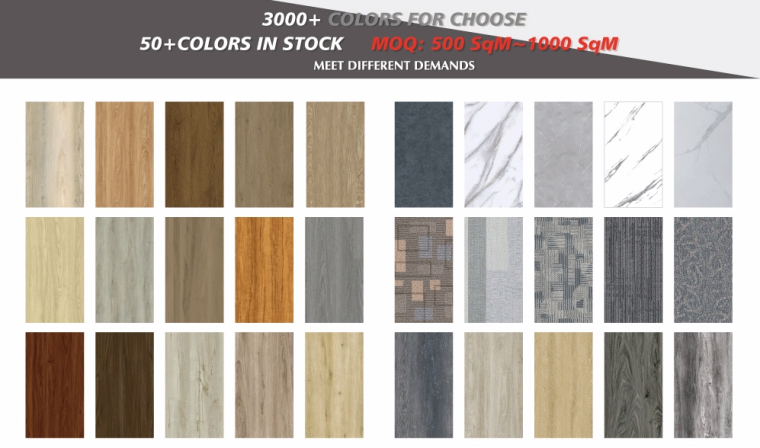
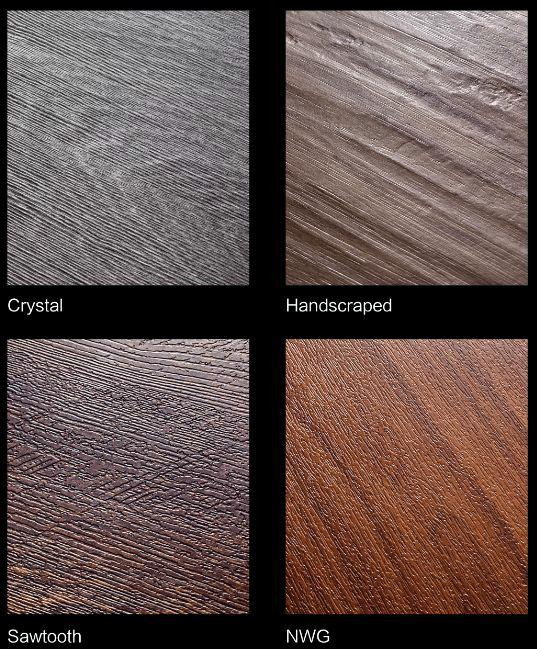
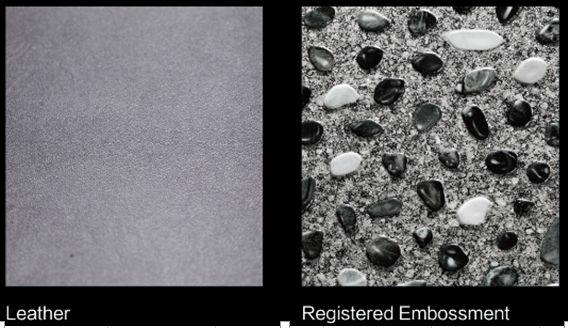
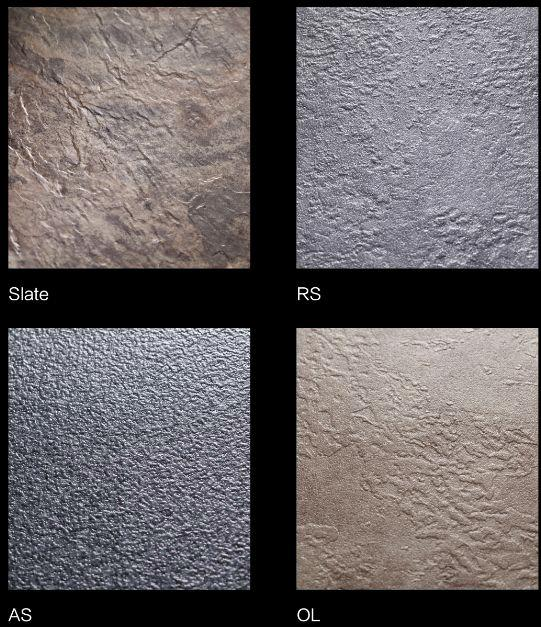
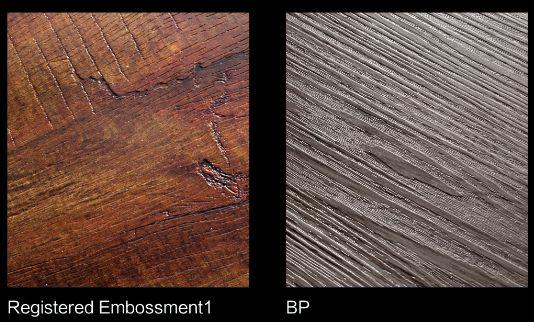
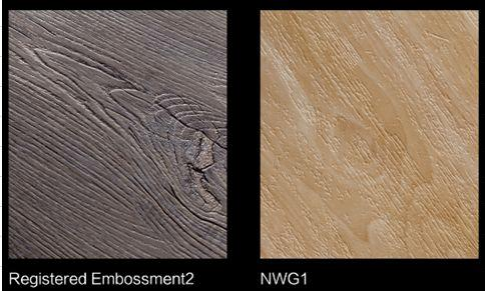
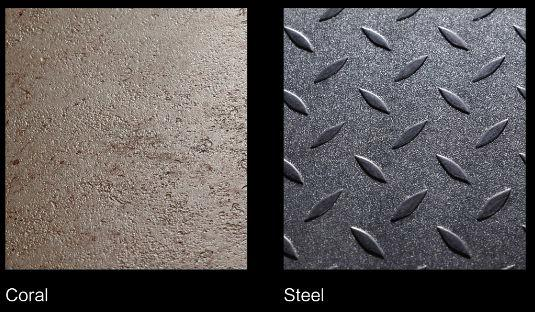
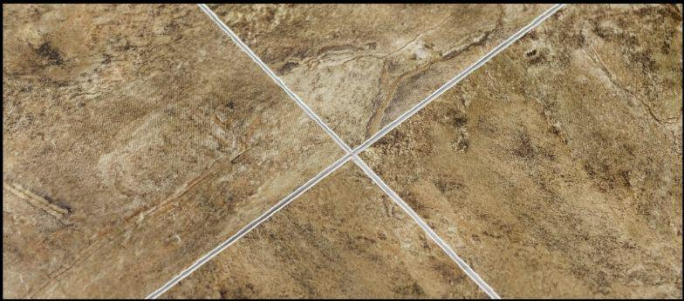
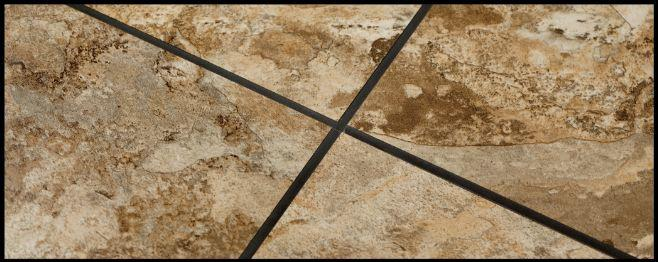
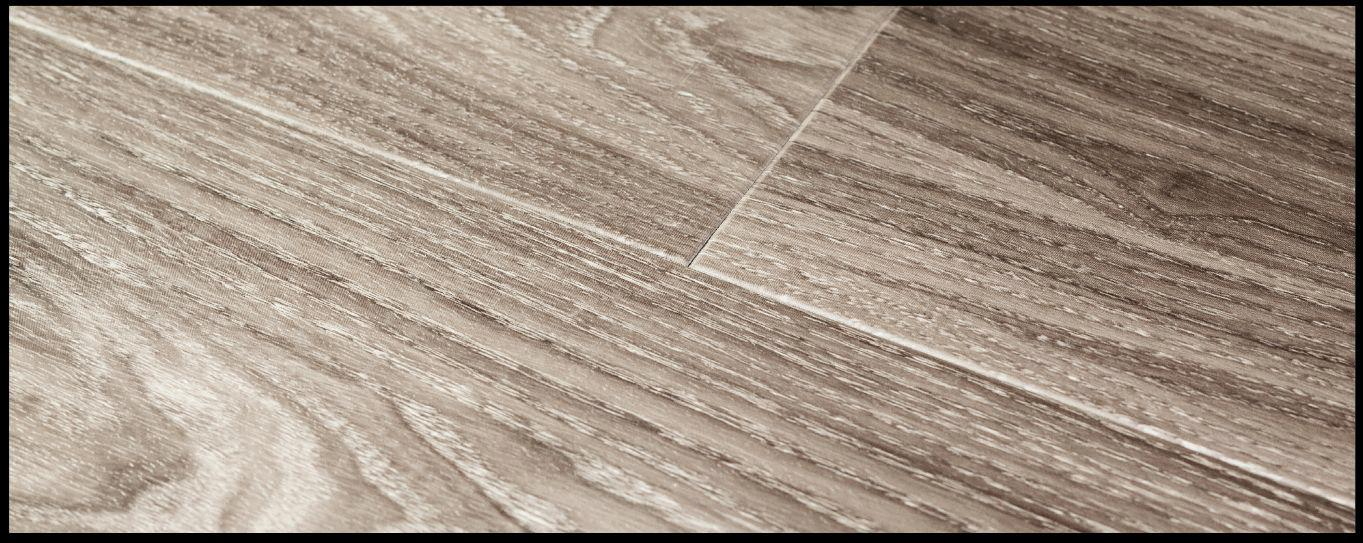
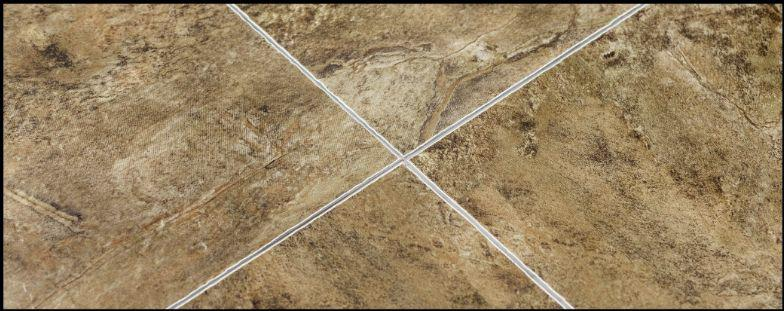
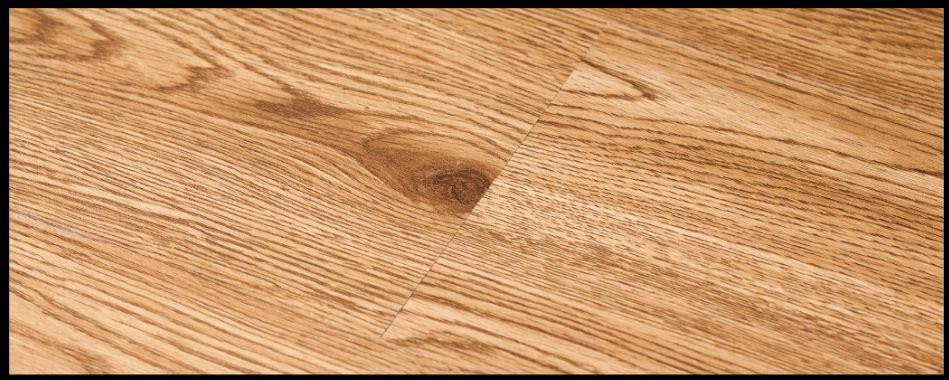
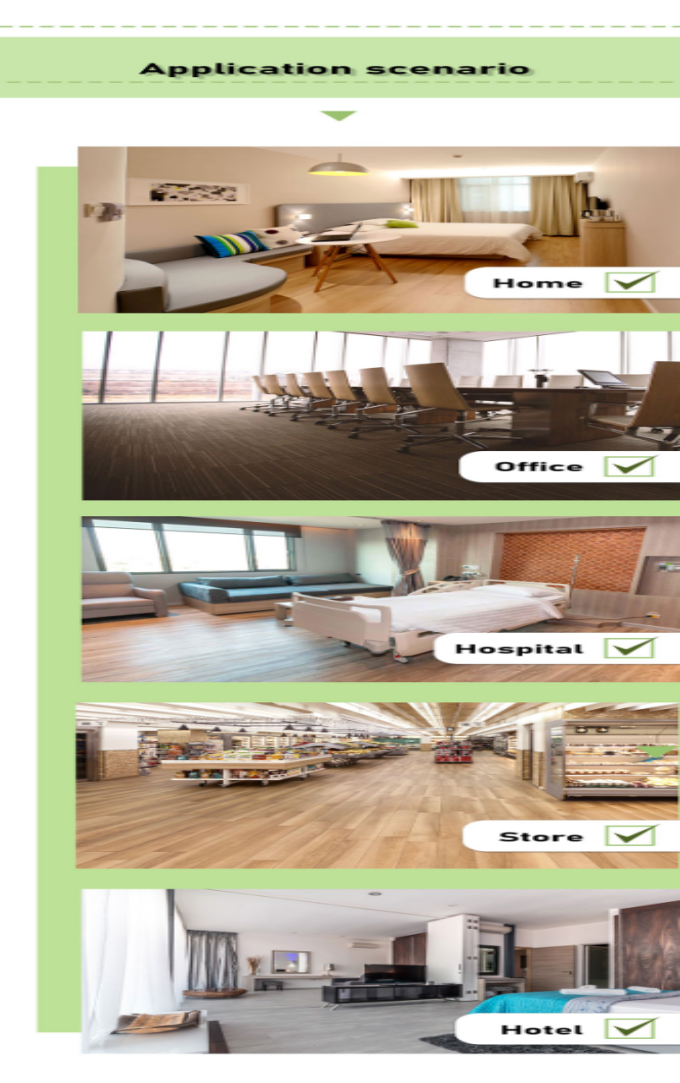
How is LVT Installed?
Glue Down application, also known as “dryback”
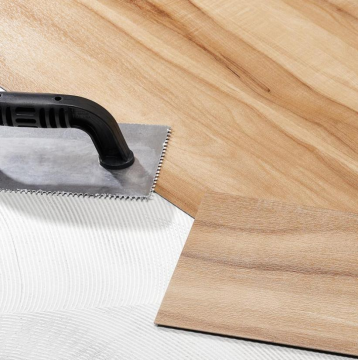
Rigid Core Click application
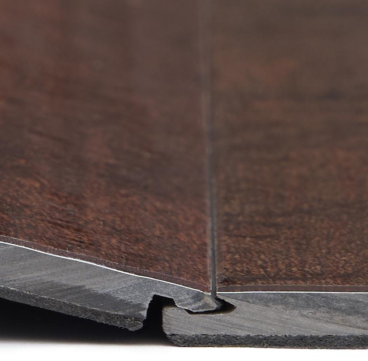
There are multiple luxury vinyl flooring constructions that have been engineered to answer the different needs in both commercial and residential spaces. Innovations in the LVT product category have made the installation process easier for home-owners and installers.
1. Glue Down: Also known as “dryback,” glue down is the most commonly used in commercial applications because of the heavy foot-traffic environments and heavy rolling loads. This installation method requires the use of an adhesive when installing. There have been many innovations with adhesives in the past 10 years beyond the traditional troweled-on application, including roll-on, peel, and stick, and spray adhesives.
2. Click: Unlike glue down, click does not require the use of adhesives, as the planks or tiles are installed by using the tongue and groove locking system on the edges of the product. This provides for a quicker and easier installation versus glue down/dry back. However, traditional click LVT has issues with sub-floor irregularities and dimensional stability, so it has mostly been replaced by the improved rigid-core click product category.
3. Rigid Core Click: This LVT has an installation process similar to the click LVT, but typically has a thicker and more rigid construction. The rigid core LVT construction provides better resistance to indentations, better dimensional stability, and added comfort-under-foot. There are 2 general rigid core categories: WPC (wood plastic core) and SPC (solid polymer core or stone plastic composite). WPC was the original rigid core construction introduced in the US market but experienced issues with product construction and dimensional stability. SPC flooring was introduced to fix the flaws that WPC flooring experienced, offering a more structurally stable and waterproof construction.
4. Loose Lay: This LVT version is a thicker product construction versus glue down (typically 5.0mm). Most manufacturers promote loose lay LVT in smaller spaces with no rolling loads since minimal adhesive is required around the perimeter. The manufacturers recommend an adhesive be applied to loose lay LVT in a medium-sized room (width of the room larger than 20 feet) on the perimeter of the room, or even a grid of adhesive every 8 feet. In applications with heavy foot traffic or rolling loads, manufacturers recommend doing a full spread of adhesive with loose lay which turns it into a glue-down installation. The benefits of loose lay are a quicker installation process, acoustical benefits, use on sub-floors with high moisture content, installation over existing floors, and more comfort-under-foot.
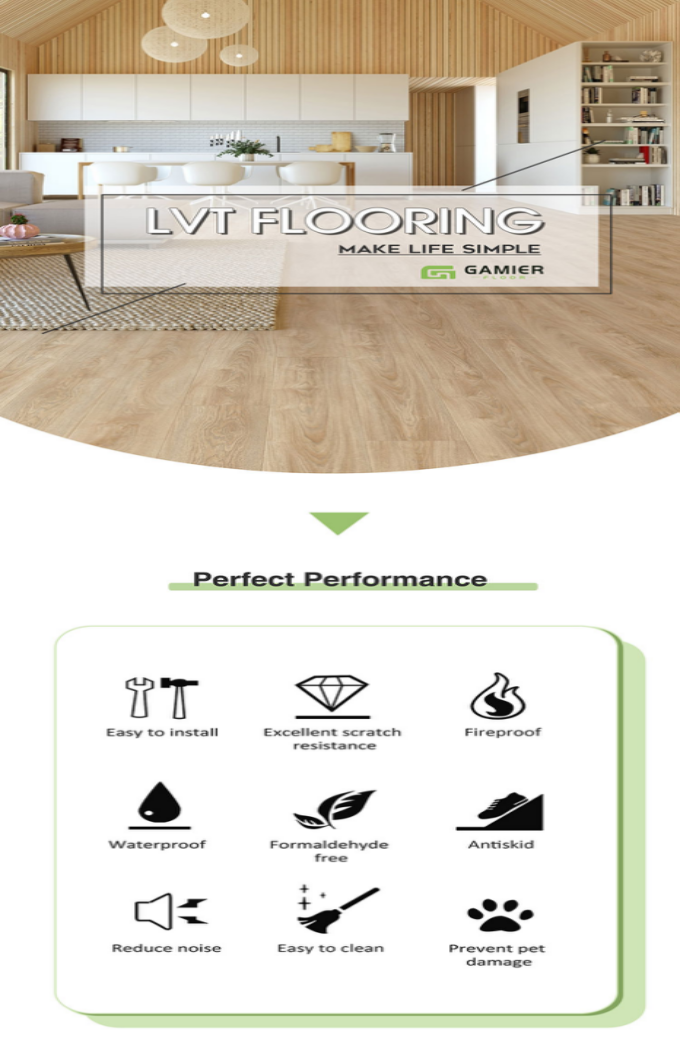
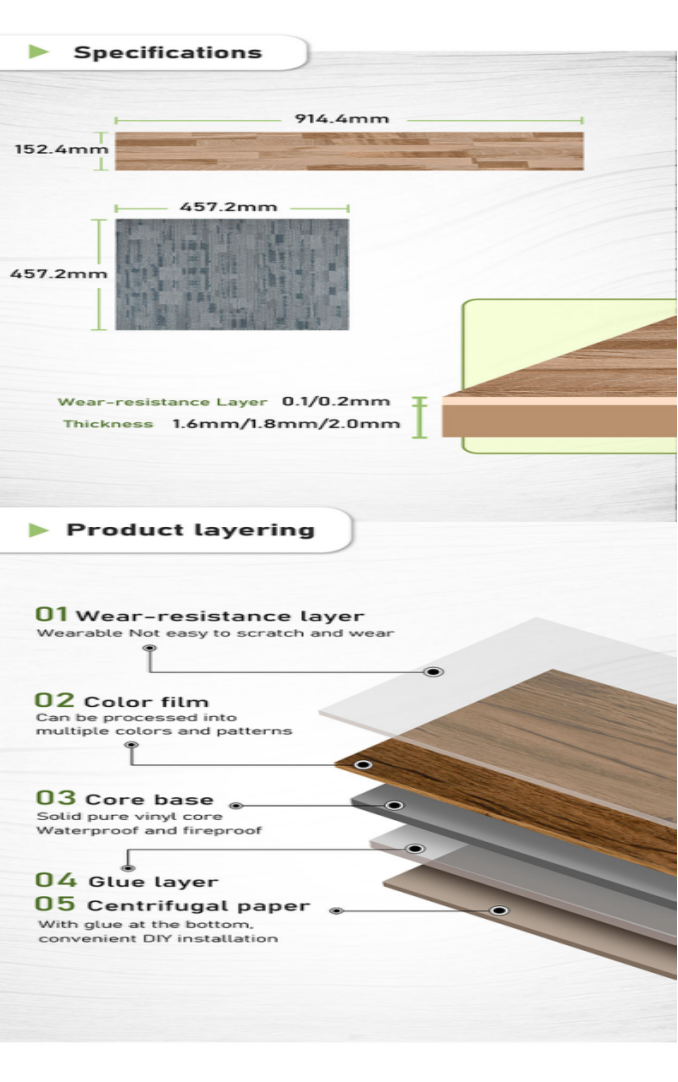
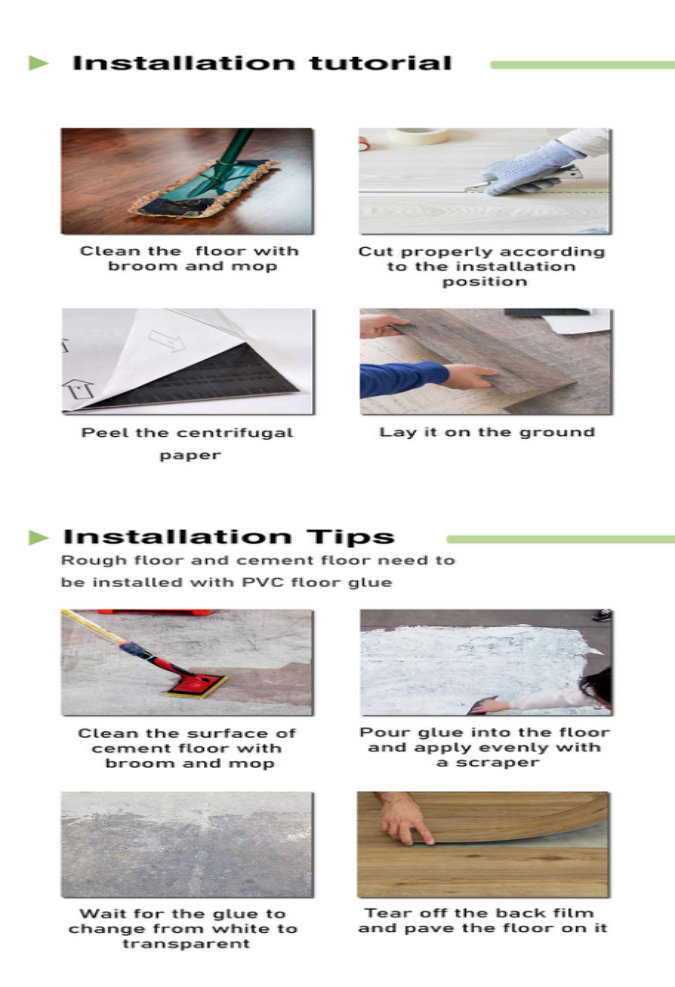
Factory View
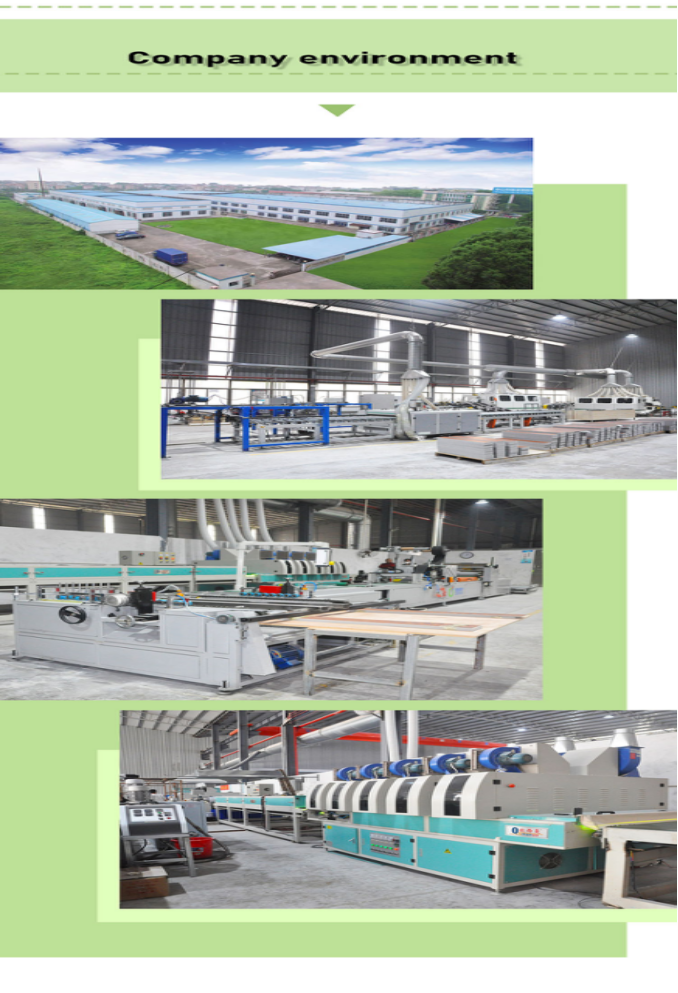

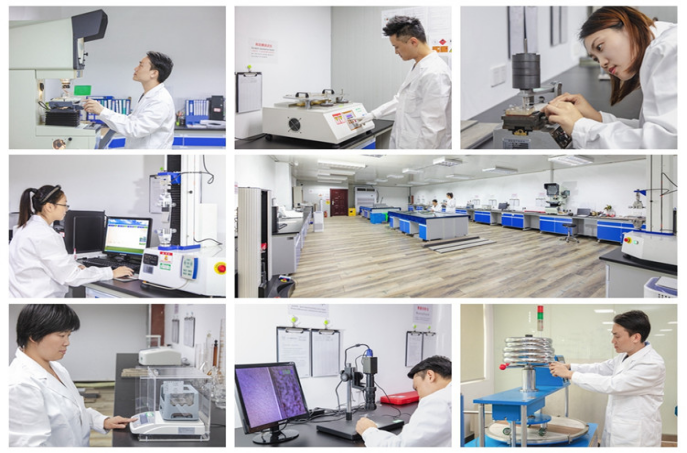
Exhibition
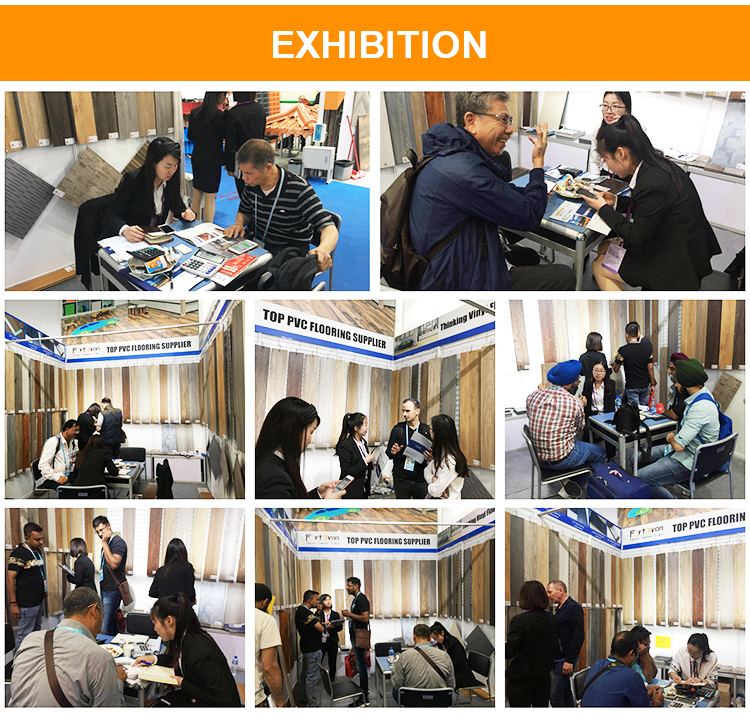
Certification
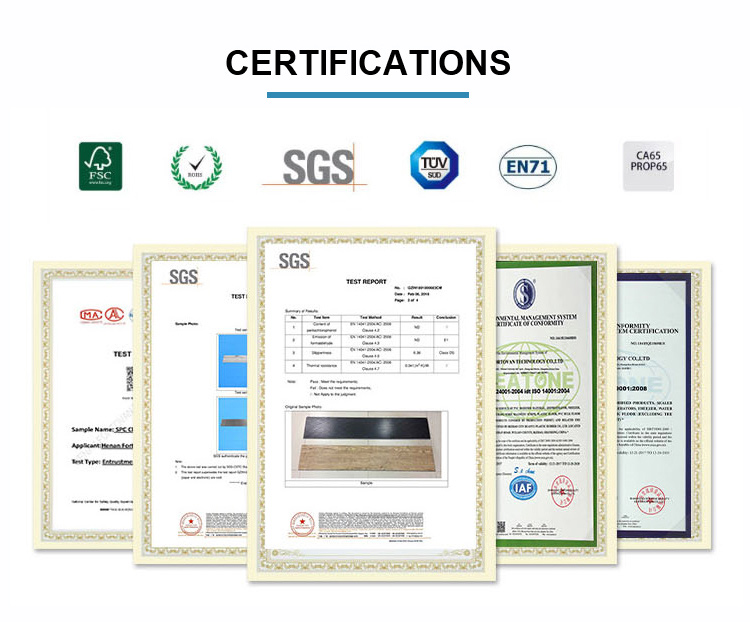
Why Choose Us
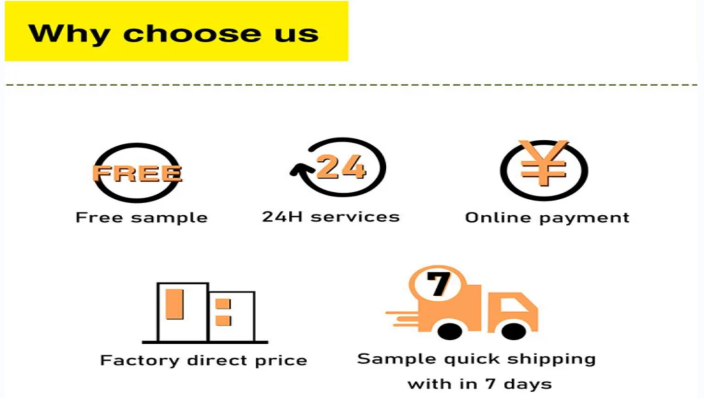
FAQ
1.How do you guarantee the quality of your PVC vinyl flooring?
Each step is strictly controlled by the QC team to make sure all our products turn out great.
Our products have a limited warranty as long as 7~15 years.
2.How about the delivery time ?
Lead time since receipt of 30% T/T deposit payment : 30 days . (Samples will be prepared within 5 days.)
3.Do you offer other products besides PVC vinyl flooring?
Yes. Besides PVC vinyl flooring we also provide as T-molding, skirting , Click system vinyl flooring, WPC vinyl flooring AND so on interior decoration material.
4.Do you charge for the samples ?
According to our company policy ,We provide free samples ,But the freight charges need customers pay.
5.Can you produce according to customers' design ?
Sure,We are professional manufacturer ,OEM AND ODM are both welcome .